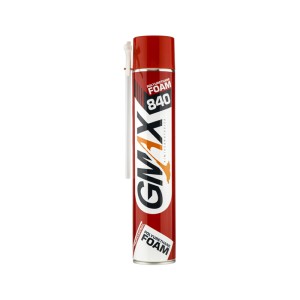
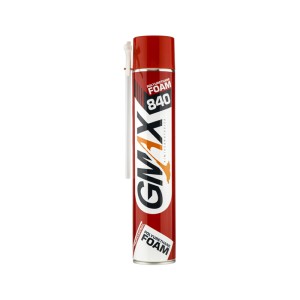
Foam Polyurethane 840
GMAX Polyurethane Spray Foam is a high-performance insulation solution, originally developed in the 1940s for military aircraft and widely adopted for general insulation in the 1970s.
Why Choose GMAX Polyurethane Foam?
✅ Superior Insulation – Ideal for object insulation, forming a strong, energy-efficient barrier.
✅ Advanced Composition – Made from polyol and isocyanate, which react and expand into a durable foam.
✅ Fast Drying & Long-Lasting – Quickly solidifies into a crack-resistant, deformation-proof insulation layer.
✅ Easy Application & Customization – Excess foam can be trimmed for a precise fit, ensuring efficiency in any project.
From construction and industrial insulation to automotive and residential applications, GMAX Polyurethane Spray Foam provides a reliable, permanent, and highly effective insulation solution.
technical specifications
Density |
23 g/ml |
Temperature resistance |
-40 c &100 c |
Free sticking time |
10 mins |
Tensile strength |
9 N/CM2 (DIN 53571) |
Shear strength |
5 N/CM2 (DIN 53427) |
Elongation at break |
20-25% |
Compressive strength |
4 N/CM2 (DIN 53427) |
Foam expansion |
100% to 200% |
Water suction |
MAX 1% |
Fire properties |
B 3 |
Heat conductivity |
0.021 w/MK (DIN 52612) |
Curing time |
20 C1 cm/hour (high humidity) 20 C0.5 cm/hour (low humidity) |
Gross weight |
850 gr |
product usage
GMAX Polyurethane Foam is an efficient and durable solution for insulation and sealing, offering superior performance across multiple industries.
Key Applications:
✅ Sound Insulation
- Reduces noise in engines, vehicles, and partition walls, enhancing comfort.
✅ Sealing & Filling
- Seals gaps between wooden panels, ensuring a tight and secure fit.
- Fills seams, cavities, cracks, and fractures around water and electrical systems, preventing leaks and energy loss.
- Seals joints between wooden and PVC doors and windows, improving insulation and airtightness.
✅ Thermal Insulation
- Enhances energy efficiency in sewer pipes, water pipes, and central heating systems by reducing heat loss.
- Provides superior temperature regulation and soundproofing in wall panels, prefabricated walls, and ceiling panels.
Why Choose GMAX Polyurethane Foam?
✔ Long-lasting & durable for permanent insulation solutions
✔ Multi-purpose application across construction, automotive, and industrial sectors
✔ Energy-efficient, improving temperature control and reducing costs
With GMAX Polyurethane Foam, achieve high-performance insulation and sealing for a more efficient, comfortable, and durable environment.
how to maintain
For safe and effective use of GMAX Polyurethane Foam, follow these important guidelines:
🛑 Personal Safety Measures:
✔ Always wear a mask, safety goggles, protective clothing, and gloves.
✔ Avoid inhaling vapors from the foam.
✔ In case of eye contact, rinse immediately with plenty of water and seek medical attention without delay.
🛑 Storage & Handling:
✔ Store in a cool, dry place, away from direct sunlight.
✔ Ensure the temperature does not exceed 50°C to prevent hazards.
✔ Never pierce or burn foam cans, even after use.
✔ Keep the product out of reach of children for safety.
By following these precautions, you can ensure safe handling and long-lasting performance of GMAX Polyurethane Foam in all your insulation and sealing applications.
How to use
For maximum adhesion, durability, and performance, follow these essential steps when applying GMAX Polyurethane Foam Sealant:
1. Clean the Surface 🧼
✔ Ensure the application surface is free of grease, dust, and debris.
✔ A clean surface enhances bonding strength and ensures a long-lasting seal.
2. Prepare the Foam 🔄
✔ Shake the polyurethane sealant spray foam for 1 minute or at least 20 times.
✔ This step is crucial to ensure proper mixing and foam quality.
3. Moisten the Surface 💧
✔ Lightly spray the surface with water before application.
✔ Moisture improves adhesion and enhances foam expansion.
4. Apply the Foam Evenly 🎯
✔ Spray slowly and consistently to maintain the correct polyurethane-to-gas ratio.
✔ Avoid spraying too quickly to prevent improper expansion and adhesion.
5. Allow to Dry & Trim Excess ✂
✔ Let the foam fully cure before making adjustments.
✔ Use a cutter to trim any excess foam for a neat, professional finish.
6. Finishing Touches 🎨
✔ Once dry, the foam can be sanded or painted for a smooth and polished look.
By following these steps, you ensure high efficiency, superior insulation, and long-term durability when using GMAX Polyurethane Foam Sealant in all your sealing and insulation projects.